Artificial Intelligence Is Changing The World, And The Cement Industry Is No Exception. Should We Be Worried, Or Is It The Time To Embrace The Revolution?
By Jonathan Rowland
We need to talk about how good AI is getting. So read a headline from the New York Times in August 2022. Since then, public interest in artificial intelligence (AI) has grown, but the headlines have taken a darker turn. AI pioneers and industry experts have warned – some in apocalyptic terms – of the potential impact AI could have on society. Politicians have held public hearings; ink and airtime have been expended in bulk, making the case both for and against. And all while money continues to flow into AI development.
Against this backdrop, Cement Products spoke to Dr. Aidan O’Sullivan, associate professor in Energy and Artificial Intelligence at UCL Energy Institute, fellow of the Alan Turing Institute, and program committee chair in AI and climate change at the International Research Center on Artificial Intelligence, which operates under the auspices of UNESCO. O’Sullivan is also chief technology officer and one of the founders of Carbon Re, which works to support decarbonization in hard-to-abate sectors, such as the cement industry, using AI. We began with his definition of this controversial technology.
“AI is a very broad term but, in a nutshell, it is a branch of computer science that leverages computers and machines to solve complex mathematical equations, mimicking the problem-solving and decision-making capabilities of the human mind,” he said. Early forms include fuzzy logic and model predictive control: technologies that are very familiar to the cement industry. Carbon Re’s expertise is in a more recent development, machine learning, a “field of AI in which the algorithms can learn and improve over time.”
The company is specifically focused on deep reinforcement learning, a “powerful subfield of machine learning that can efficiently interact with complex systems and apply sophisticated strategies to solve intricate problems. This is an area of AI that has seen considerable breakthroughs in recent years, such as in protein folding and in natural language models like ChatGPT.”
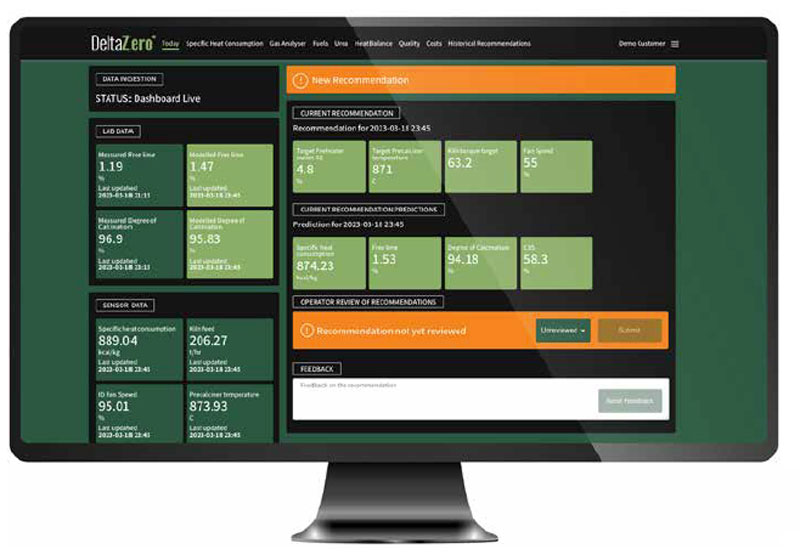
An Industry Ripe for an AI Transformation
Although machine learning has been the subject of decades of research and millions of dollars invested, it is a technology that – unlike fuzzy logic and model predictive control – has yet to make a significant impact on the cement industry. “There were no industry-specific solutions available,” explained O’Sullivan. “However, thanks to Industry 4.0 initiatives, the cement industry is progressing its digitalization journey significantly and is now successfully capturing and collecting the data needed for machine learning technologies.”
The complexity of the cement-making process also makes it “particularly well-suited to machine learning solutions,” he continued. This is due to the “sheer amount of data points generated per second at cement plants, as well as their complex interdependent systems. From the coolers to the pre-calciners, everything interacts together. But analyzing this complexity to any depth is almost impossible without machine learning, due to the manpower and time required, and the limited number of trained process engineers in the cement industry.”
The biggest opportunities for AI in the cement industry thus arise in the areas of cement production that produce the large, complex datasets that are best suited to computing analysis, such as pyroprocess optimization, grinding and blending of supplementary cementitious materials, logistics, and predictive maintenance.
Taking the first of these, “using AI to optimize the pyroprocess not only reduces carbon emissions, fuel consumption, and fuel costs; it also enables the plant to reduce time spent outside operational limits,” explained O’Sullivan. “It enables operators to operate the kiln within recommended quality settings and to keep NOX emissions within control limits. Furthermore, the ‘digital twin’ offers future exciting opportunities to better understand and address maintenance issues with the plant, such as kiln blockages, as well as to evaluate how best to make capital investments.”
AI can also support operators to identify and deal with sensor failure or miscalibration. As part of its work, Carbon Re spends a lot of time on data quality and validation. “This allows us to automatically identify if a sensor has failed or is giving erroneous readings, and to make an operator aware of this. In some cases, we can also provide an estimate of the true value of this sensor, based on other variables that are strongly related.”
AI and Decarbonization
Another area where AI offers significant benefits is in the cement industry’s transition to net zero.
“There is no silver bullet for decarbonizing the cement industry; a toolkit of technologies will be needed for the industry to tackle this challenge,” O’Sullivan began. “We know that specific heat consumption, and therefore specific carbon footprint, per tonne of clinker can vary significantly from one day to the next, depending on the interactions between different raw materials, operational settings, types of fuels, and specific kiln properties. This variation can have a significant impact on fuel cost and on fuel-derived emissions, which is why optimized performance is crucial for any cement plant. AI-powered optimization captures these complex relationships and can recommend optimal plant parameters to optimize fuel use and carbon emissions, while maintaining throughput and clinker quality.”
Process optimization is thus a “very effective – and relatively easy, low cost – starting point for decarbonizing cement production,” continued the Carbon Re executive. Moreover, “AI embodies two of the necessary characteristics needed to accelerate industrial decarbonization: speed and scalability. AI solutions are commercially ready, scalable, and can be deployed in plants today, to start reducing emissions now. Additionally, as soon as new AI models are available or existing models are improved, they can be immediately released and can be scaled globally.”
AI technology will also be essential to the deployment of carbon, capture, utilization, and storage (CCUS) technologies. “More than any other industrial sector, the cement industry relies on CCUS in its pathways to reach net-zero,” noted O’Sullivan. “These technologies – which have yet to be proven at scale and are not yet commercially viable – present significant complications to operational control that will need AI-enabled assistance to operate viably and economically.”
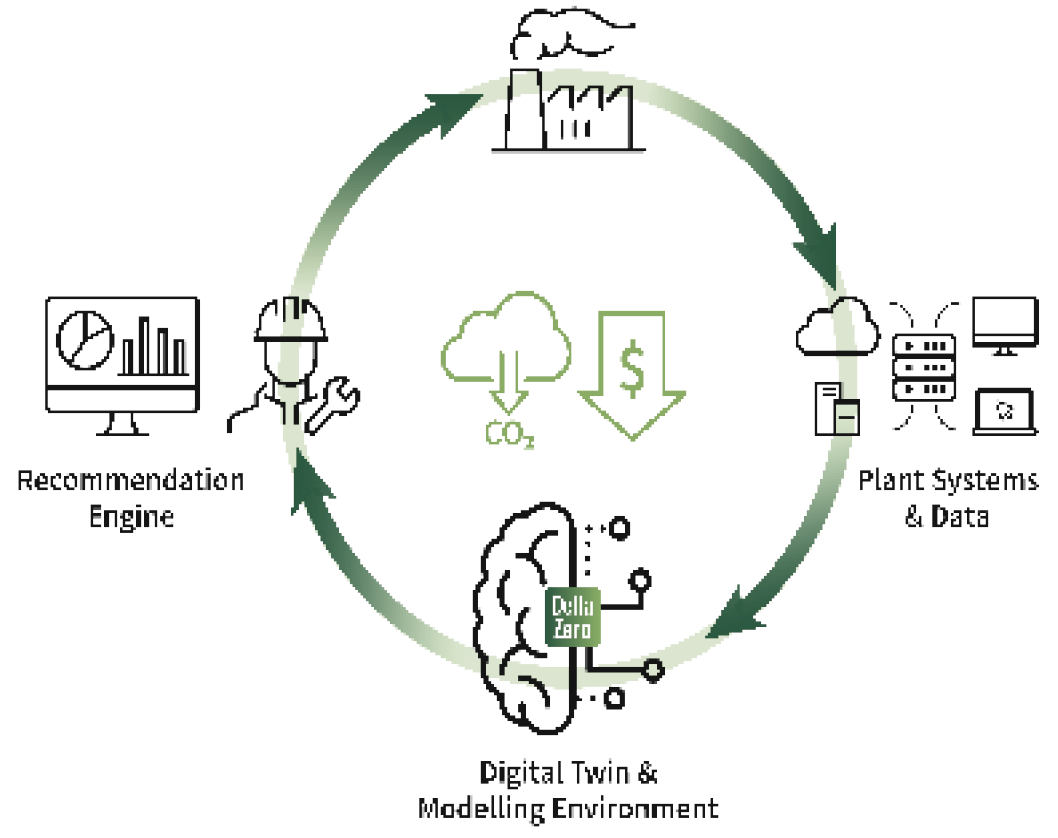
Delta Zero Cement
Carbon Re’s own AI solution is Delta Zero Cement, which combines O’Sullivan’s expertise in AI and machine learning with research on cement production carried out by Dr. Daniel Summerbell, the company’s chief solutions officer and a visiting industrial fellow at the Institute for Manufacturing at Cambridge University.
“Delta Zero Cement simulates the chemical and physical processes at a cement plant, enabling our AI agents to find tailored solutions,” explained O’Sullivan. “Each AI model is a bespoke digital twin of a cement plant. It provides dynamic and real-time process optimization, based on live data, with models continually retrained to match actual plant performance. The software considers quality metrics, such as clinker free lime, and defined operating limits, such as lower and higher precalciner temperature bounds, to provide clear, quantified recommendations that reduce the mass of CO2 emitted per useful heating value (kgCO2/UHV). This enables lower fuel costs and lower emissions.”
The system is designed to work with both manual kilns and kilns with automated process control or expert systems. It connects directly to the plant via a secure API interface, providing the AI agents with access to the live status and data of the plant.
“We have designed Delta Zero to operate either as a ‘human-in-the-loop’ or ‘closed loop’ solution,” continued O’Sullivan. Human-in-the-loop describes situations where the plant operator maintains control over production processes, supported by specific and quantified predictions and recommendations generated by the AI software. This is necessary where the kiln is manually controlled. When desired by the client, however, Delta Zero predictions and recommendations can be directly fed into an expert system by the client to optimize the process in a closed loop system. “For example, Delta Zero can feed a new quality prediction directly into the expert system every 15 minutes, or a temperature setting into the loop control. This enables the expert system to optimize the process in real time, rather than relying on delayed and infrequent laboratory results.”
Delta Zero Cement is already live in plants across Europe and South America and has previously undergone pilot studies in plants in Asia. “We are seeing really exciting results, including improvements in stability and quality, and will be releasing full case study information soon,” noted O’Sullivan.
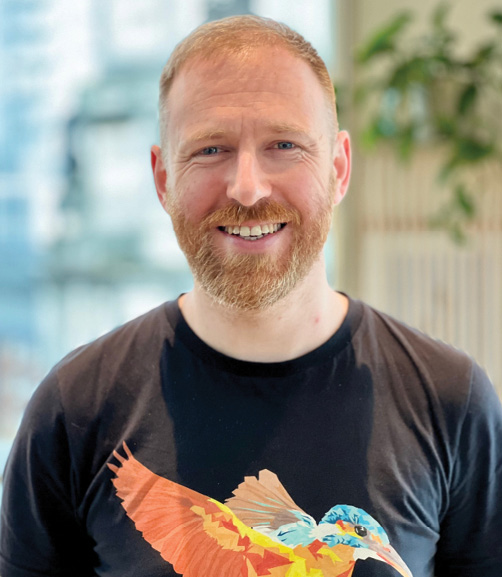
A Safe Solution?
There’s “no doubt” that the speed and power of the recent AI tools are “unlike anything we’ve seen before,” acknowledged O’Sullivan. “There are unknowns when it comes to the societal implications of generative AI systems, such as GPT-4. But language and image platforms are not representative of all AI.
“There are numerous other fields where the complex data modeling and simulations enabled by AI allows us to address fundamental issues, such as climate change and healthcare, gain a deeper understanding of scientific principles, and develop new technologies and materials.
“AI has the potential to change the world for the better across every aspect of industry, the economy and society. But it’s up to us to make sure that its development benefits people and the planet.”